Available for around $130 on AliExpress (including shipping) or from the manufacturer store, Airbank D13 Puffer Pro is a battery powered two-stage pump that delivers up to 20 psi (1.4 bar) of pressure. Note that there is also a cheaper version without the battery that requires a 12V power supply.
Contrary to the manufacturer specification on the web, this pump actually does support USB-C PD3.0 and QC3.0 power output and charging up to 30W. The included paper manual correctly states the supported USB-C voltage and power levels.
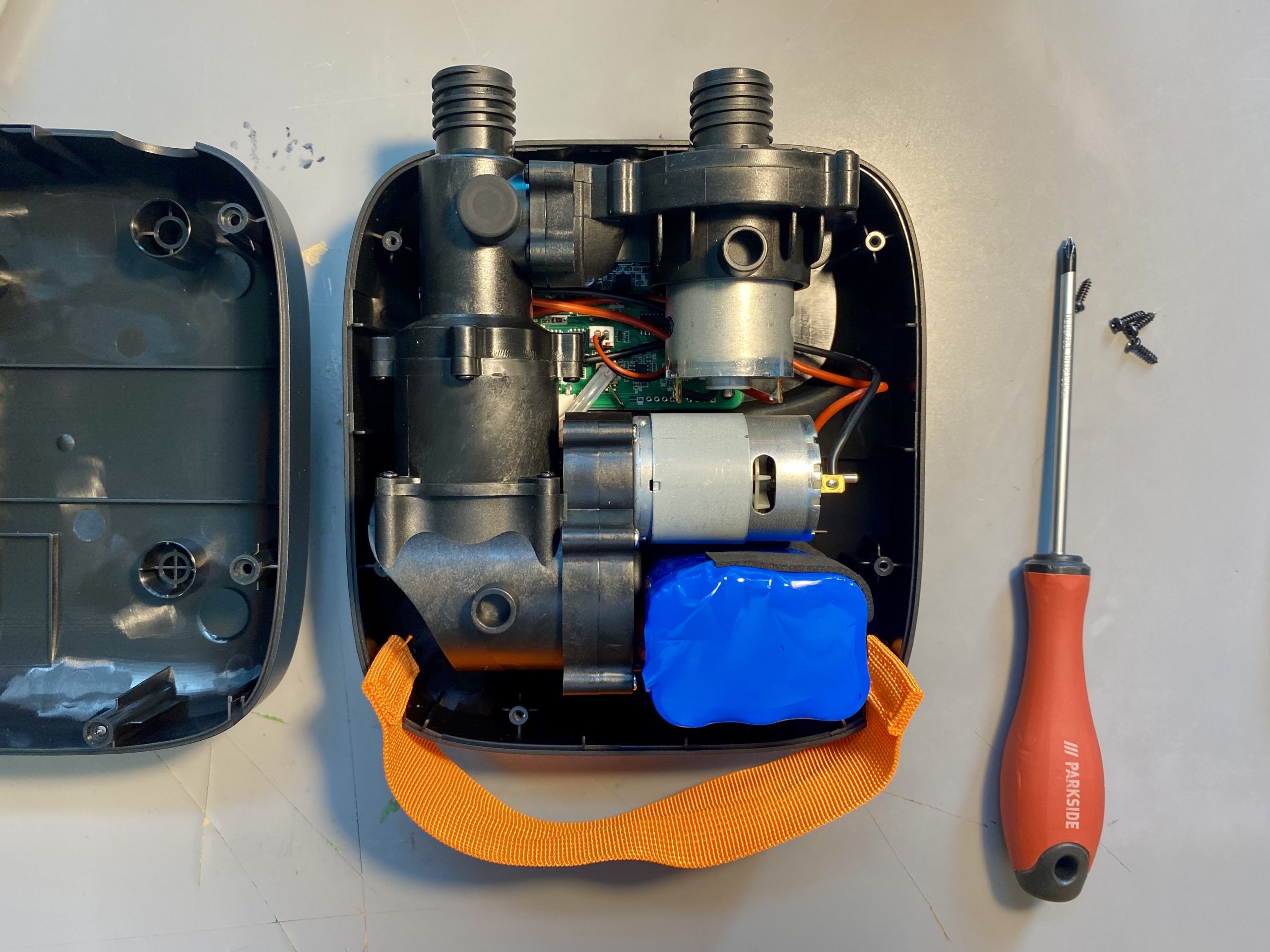
Opening the pump is really easy with just six phillips screws at the back. Inside, everything is neatly laid out and with wires of the appropriate gauge and latching connectors for the pump and battery connections, along with some adhesive to keep them secure during transportation.
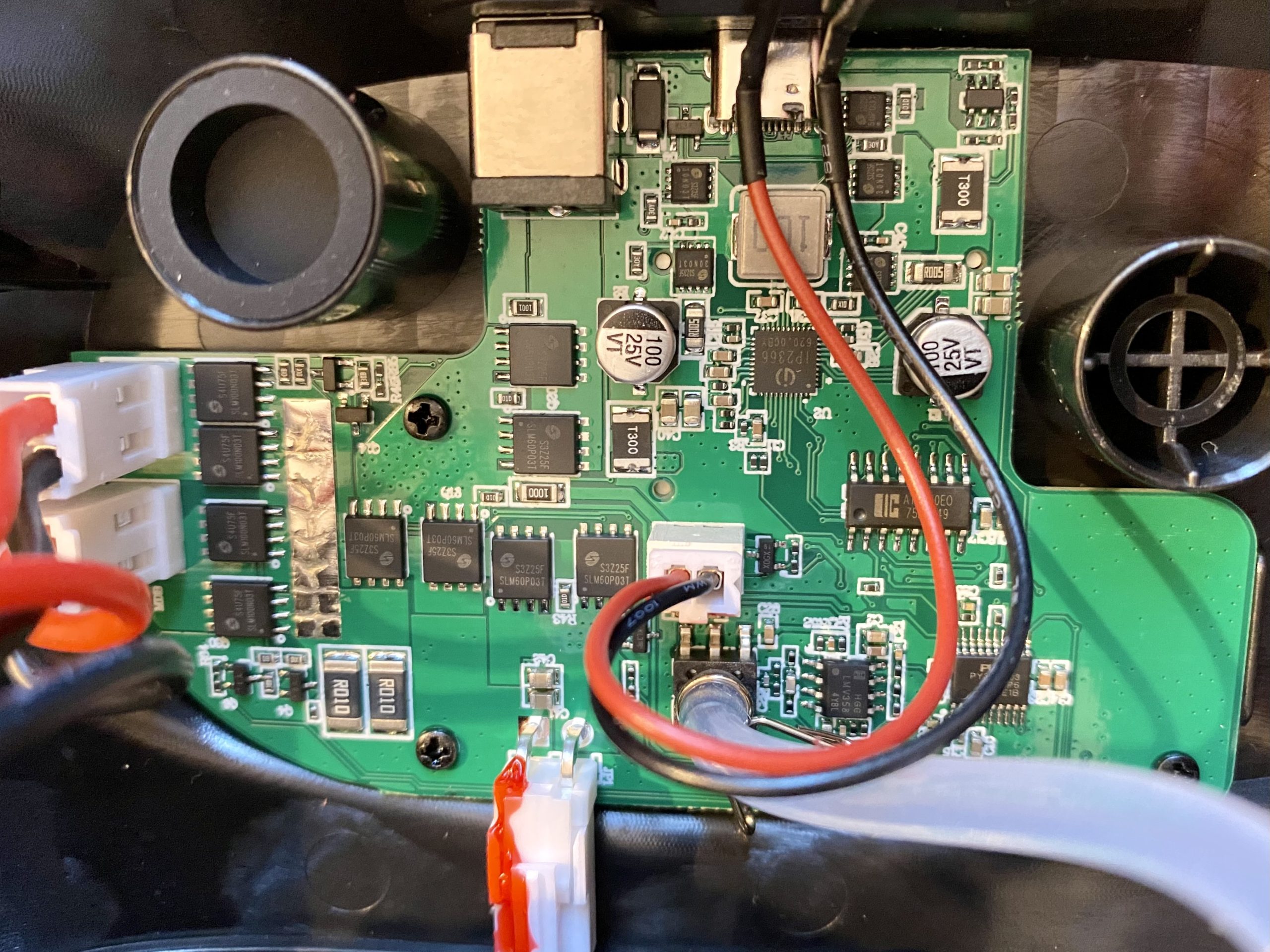
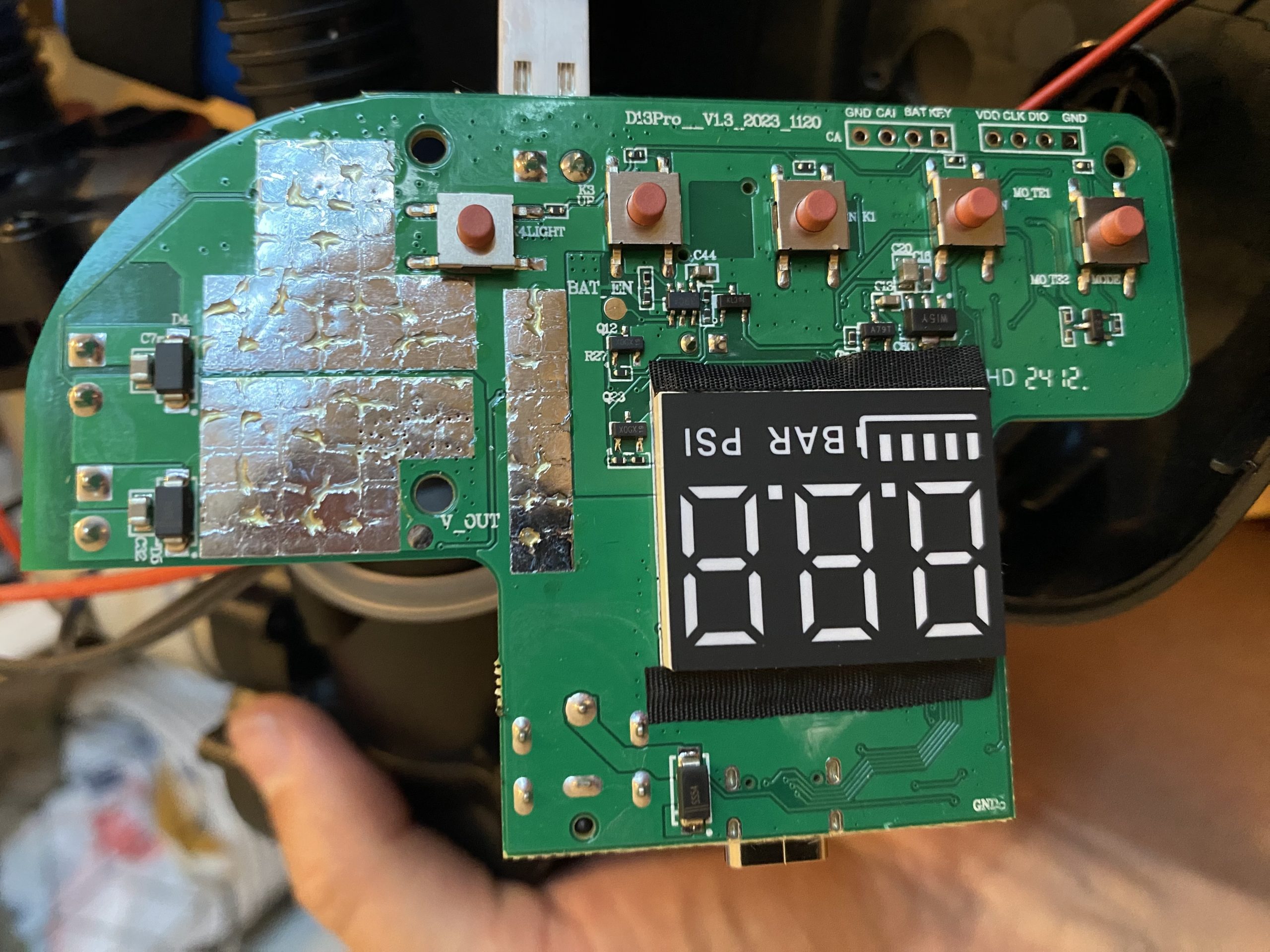
D13Pro__V1.3_2023_1120
) with the display and control buttons, and programming or debug pin connections.Pump and Compressor
There are two motors inside — one for a simple fan and another one for driving a piston pump for the high-pressure stage (above 0.8 psi). Interestingly, the fan mode uses 8A at 11V compared to just 4A in the high-pressure mode as shown in this video (be aware of the loud audio):
Battery
It features a pack of six 18650 Li-ion batteries in 3S2P configuration (3 in series, 2 in parallel) with the combined capacity of 57.72Wh (5200mAh at nominal voltage of 11.1V).
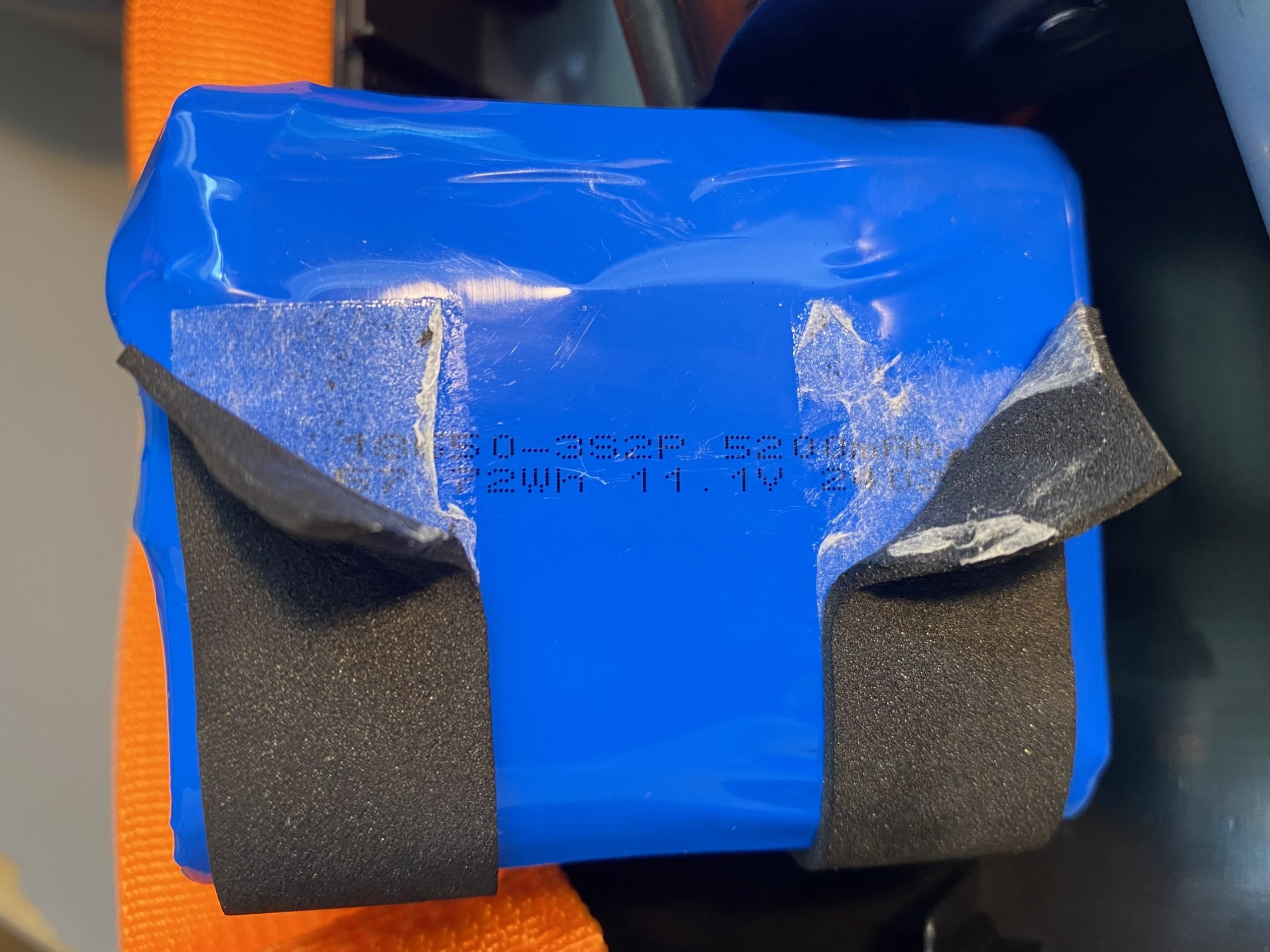
USB-C Output
Turns out it actually does support USB-C PD 3.0 charging and output up to 30W at 20V in addition to Quick Charge 3.0 (QC3) with up to 12V and 3A (36W) output thanks to the INJOINIC IP2366 power management chip.
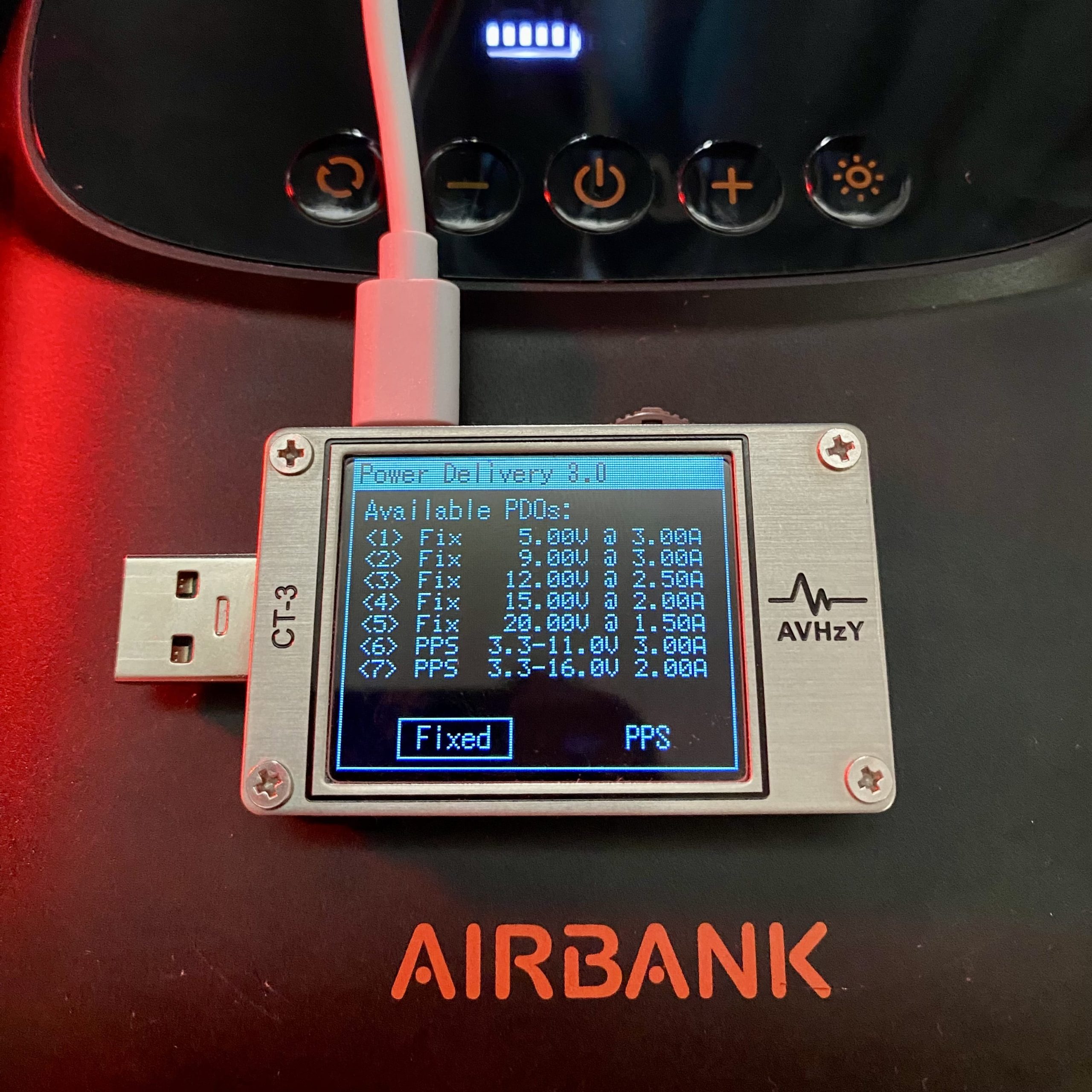
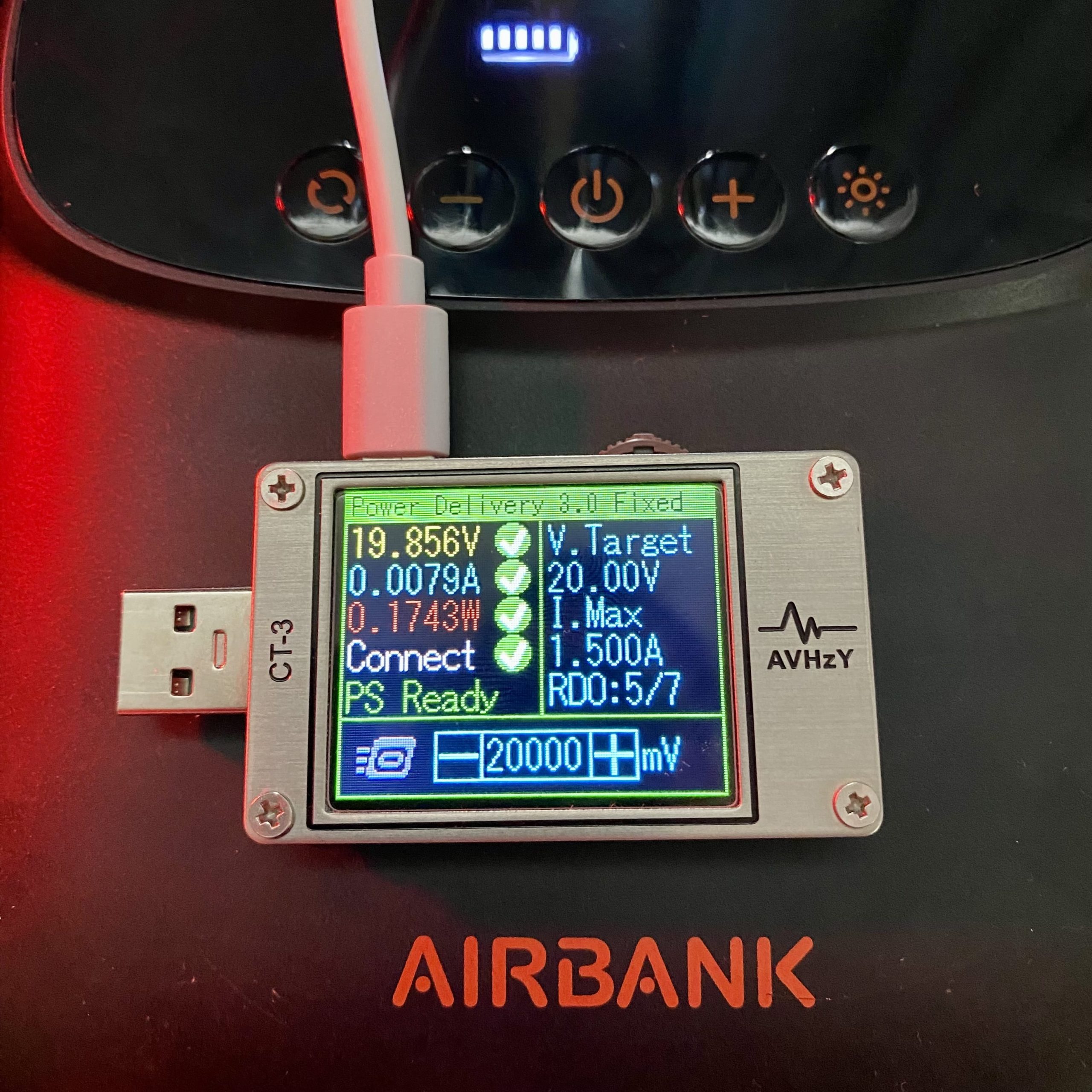
Charging
Charging over USB-C supports PD3.0 30W input while the included charger GQ20PD02-ZG can only deliver QC3.0 20W at 12V/1.67A. It would take either 2 or 3 hours respectively to fully charge the battery.
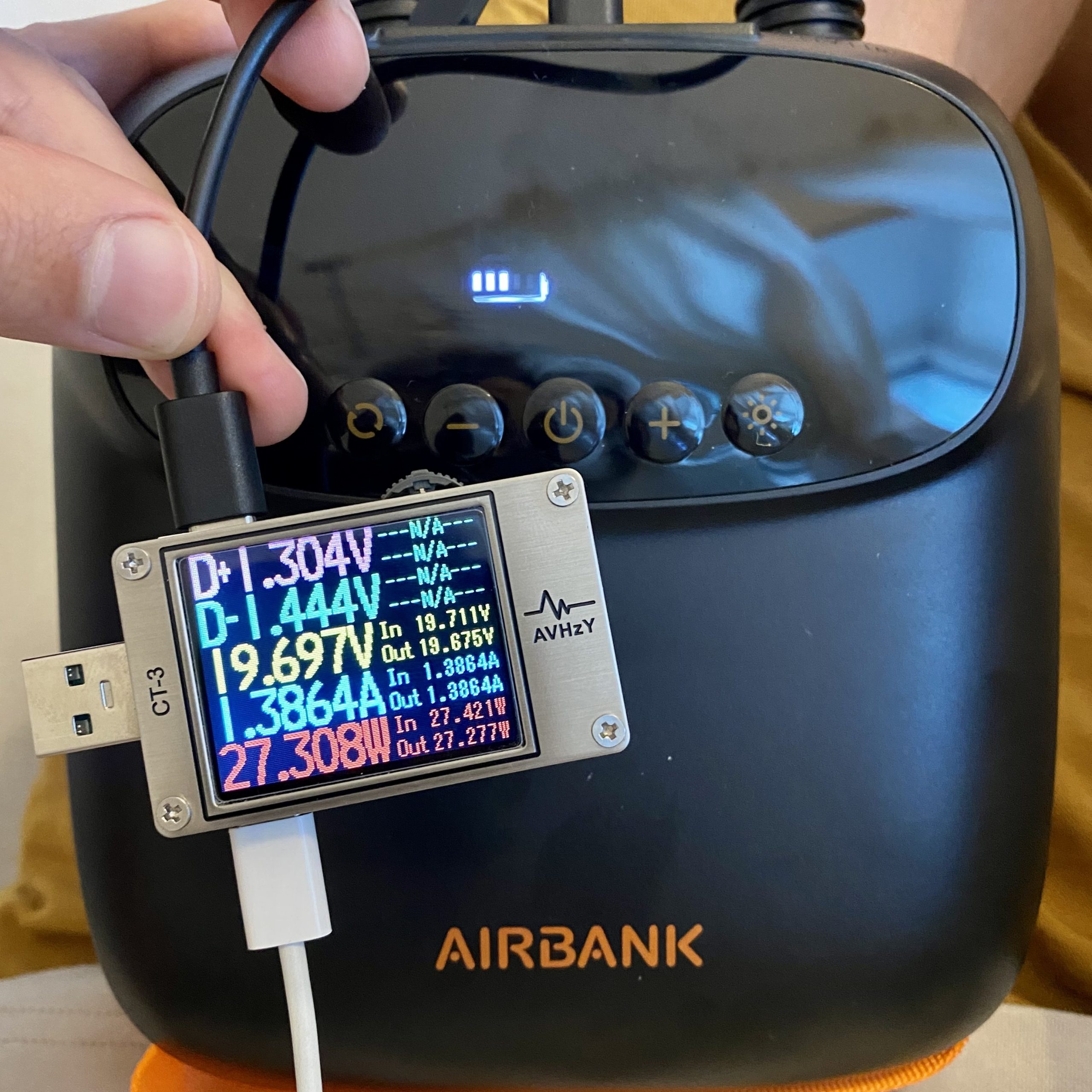
Charging Error EE3
Having played with the supported USB mode enumeration, I tested the pump performance with an actual 10’4″ (317cm) SUP and was able to bring it to 18 psi twice, including the deflation.
When attempting to charge it with the supplied USB-C charger and cable, I was now suddenly getting a message EE3 on the screen and it wouldn’t charge when left over night. I was able to fix the issue by removing and re-attaching the battery which presumably reset the controller state. Since this is not an easy operation for an average user, I’ve reached out to the manufacturer to confirm alternative solutions for resetting the device.
Photos
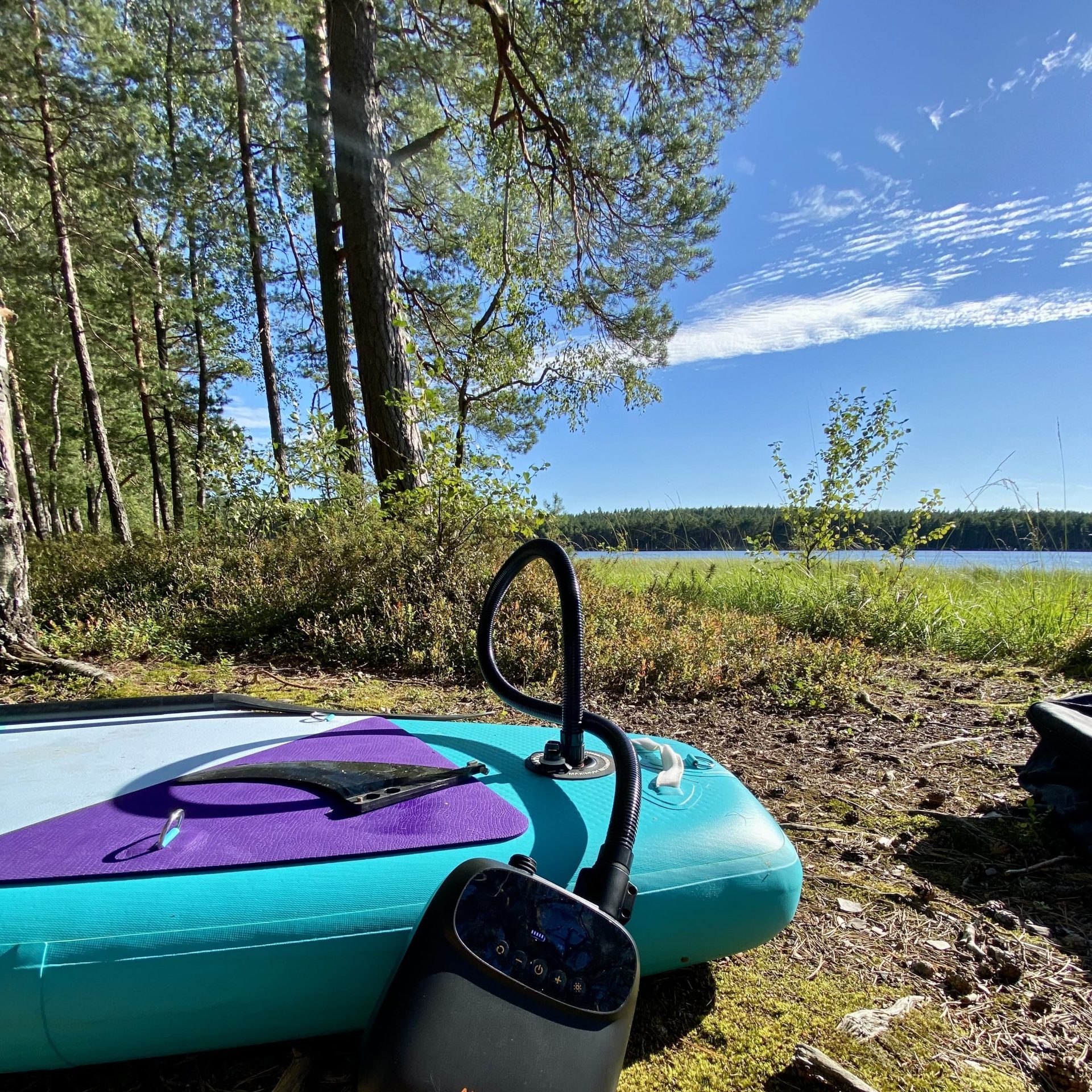
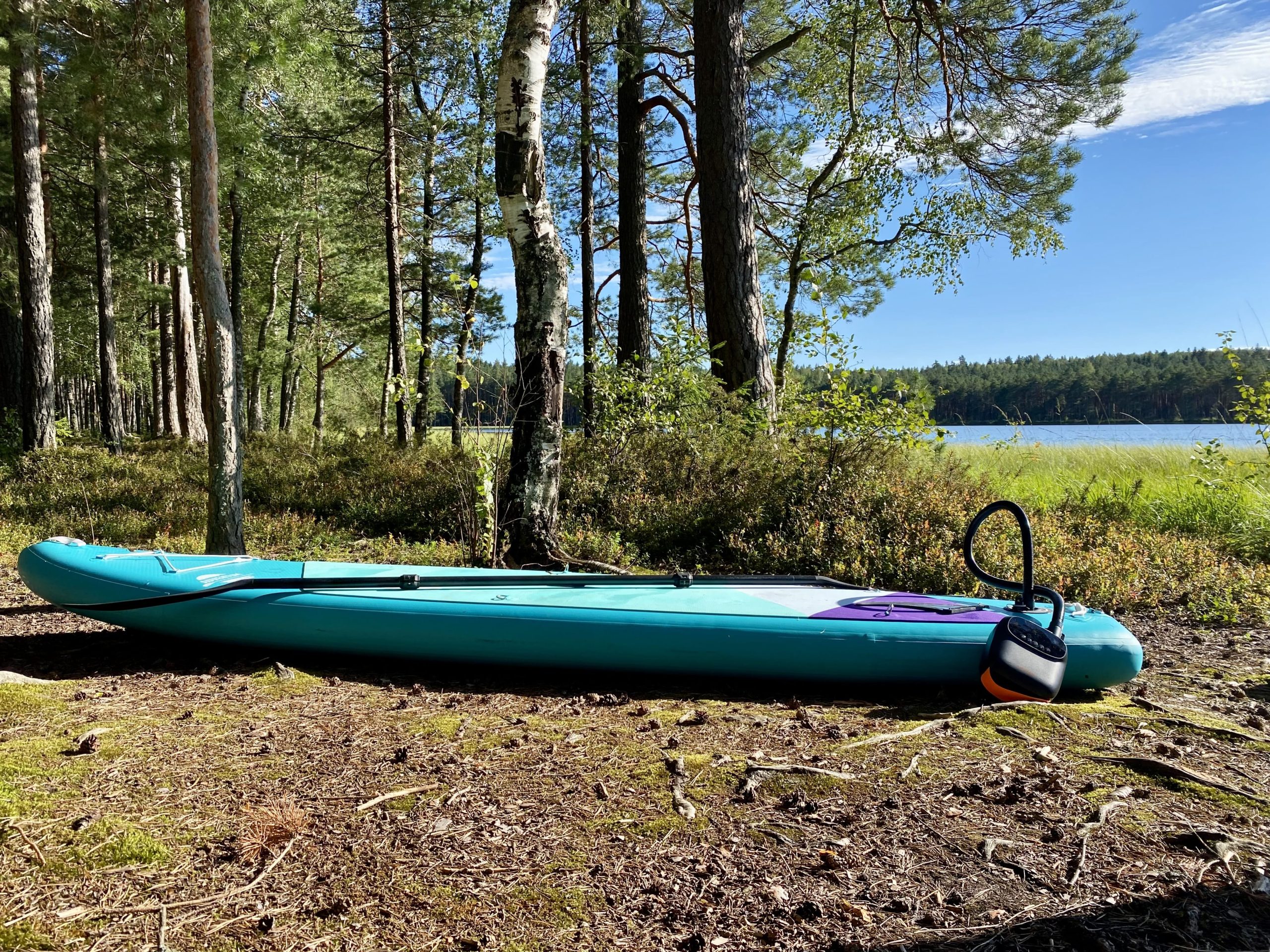
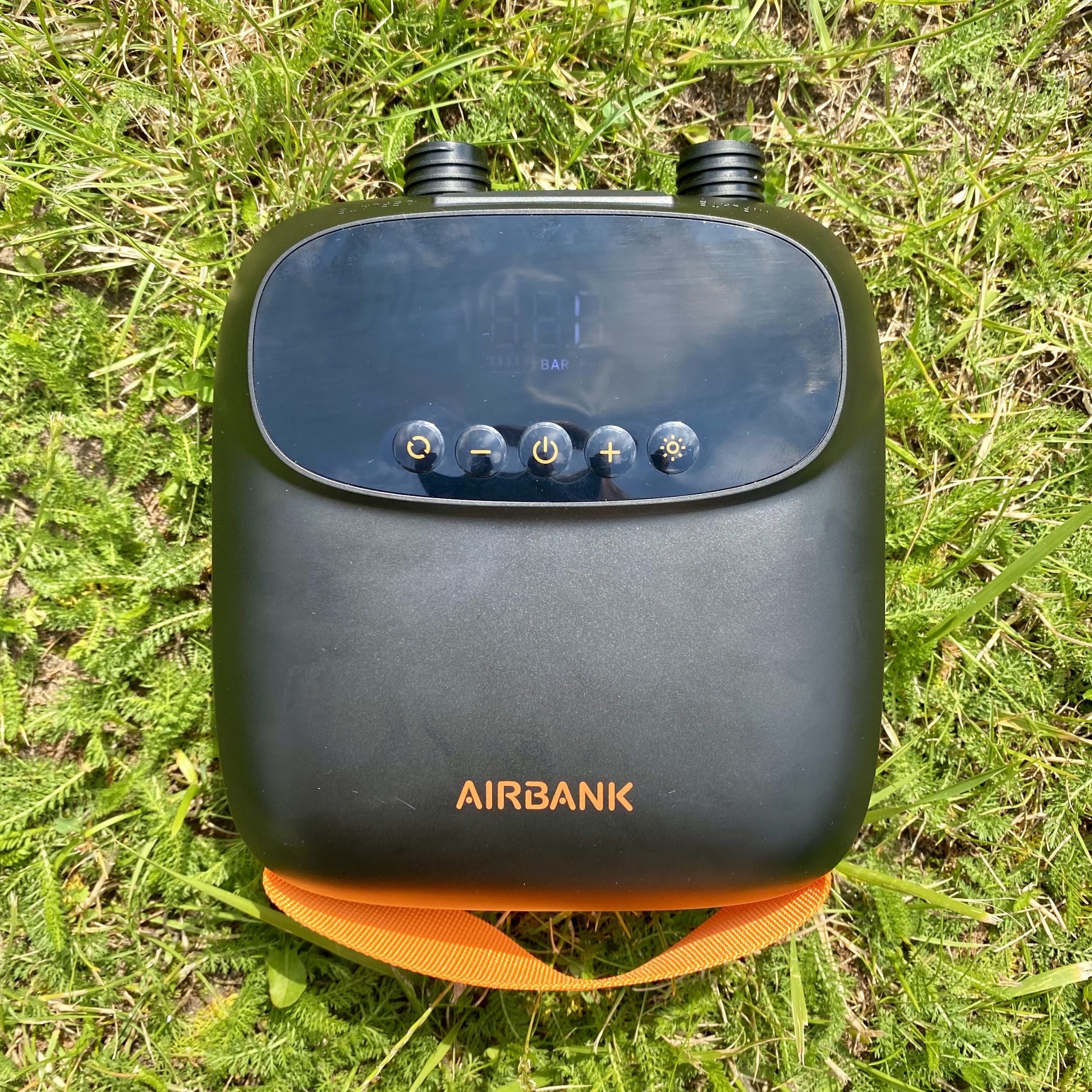
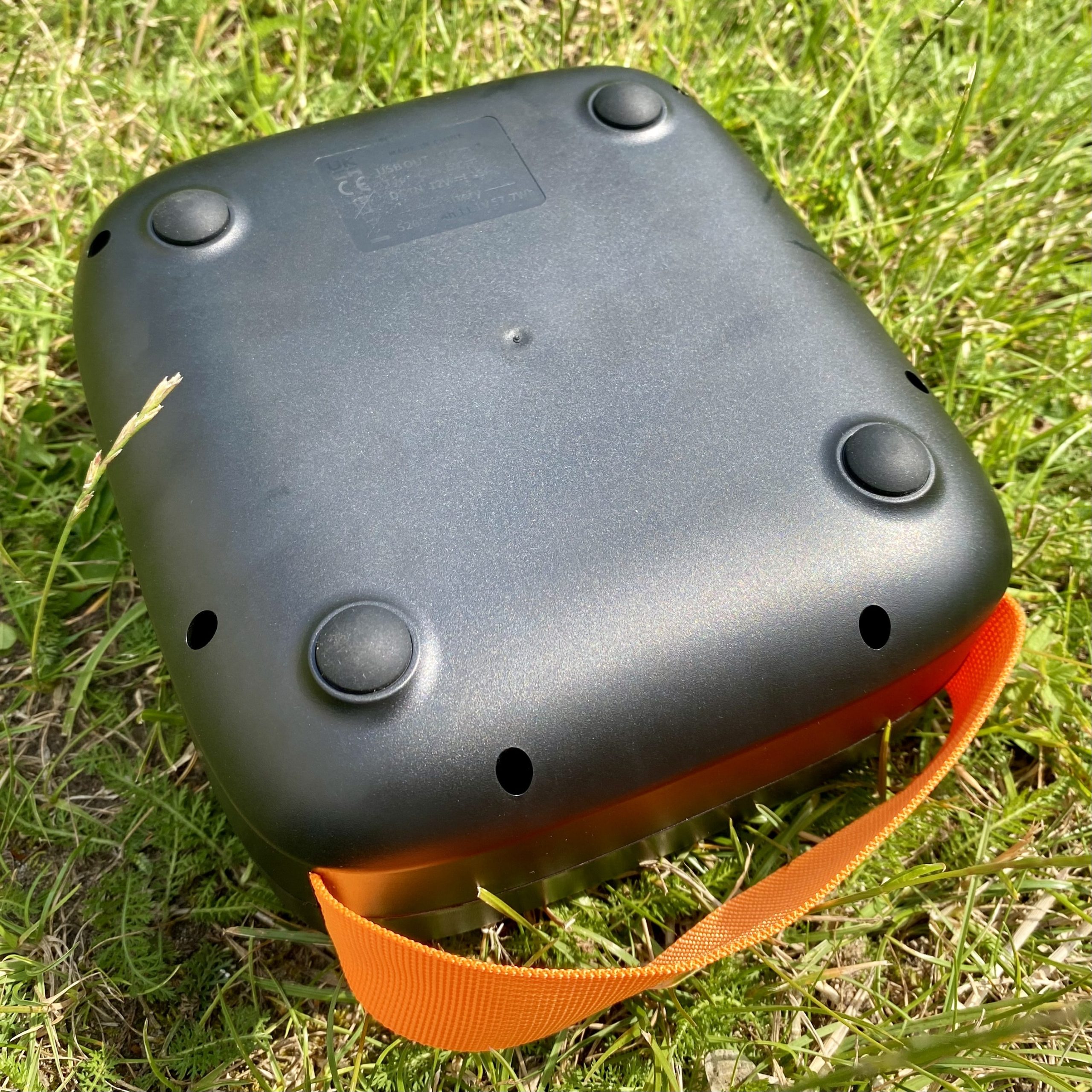
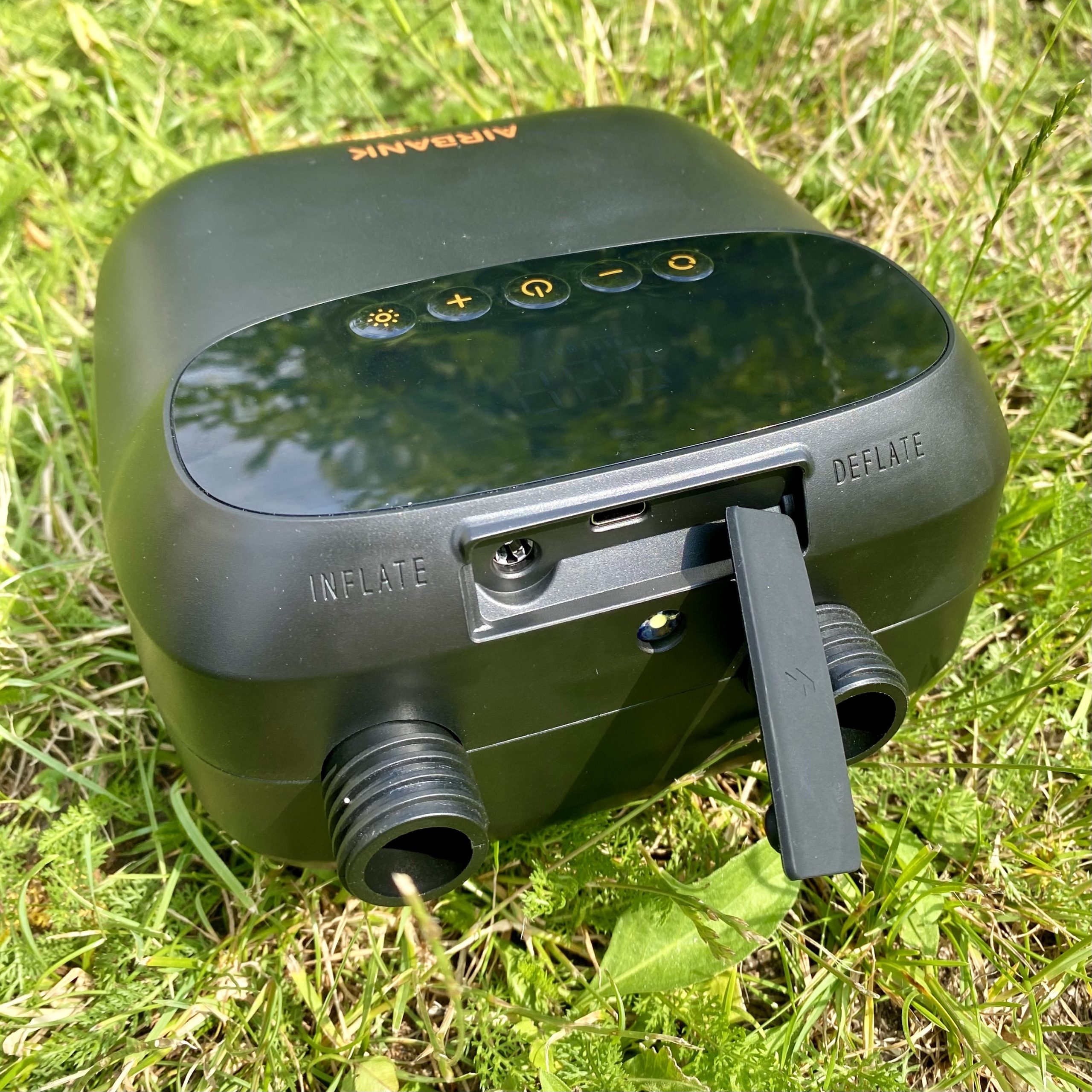
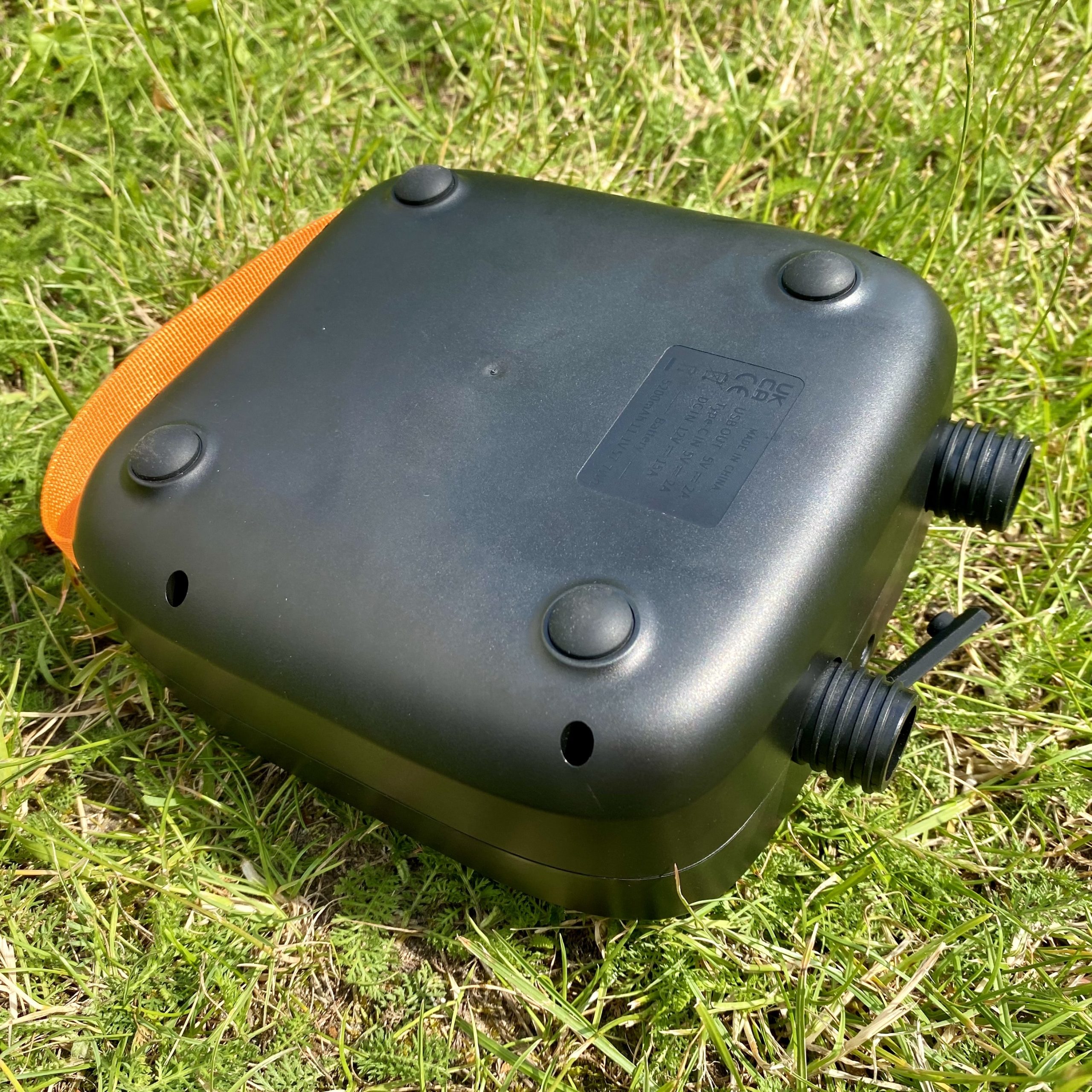
Thanks for the teardown. The one I have no longer holds a charge. Now I know what batteries to get. I have not ever built a battery pack, but there has to first time. I assume I get the flat top batteries and solder them together using what ever the old batteries have.
You would need a pack of 6 Li-ion batteries of 18650 type in 3S2P configuration which provides 4.2V x 3 = 12.6V combined voltage when fully charged.
Importantly you would also need to attach a battery management system (MBS) to the pack to control the charging, discharging and balancing of the cells since the pump control board doesn’t handle that.
Hi I have a probank puffer pump & need to replace the circuit board which started to melt the USB terminals it totally overheated could’ve even caught fire.
I see the circuit board which you are showing doesn’t seem to be the same circuit board as what I have. Do you know whether I can replace this? I can send a photo if required but grateful for your help.
I would recommend you reach out to the manufacturer over their support email — they were quick to respond.
Hi
What were the manufacturer’s advice to correct the charging error?
Yes, they responded with “please try to test again if the air pump can charge properly after draining its full capacity. [..] we have had feedback from previous customers that they never encountered an error message again when charging the air pump after draining the full charge.”
How exciting to find that someone has already torn-down this eact sup pump! I am so appreciative of the interior photos. My goal is to reduce the noise output from my Puffer Pro, and I am wondering how much space there is inside the case to potentially line some of the interior plastic surfaces with a self-stick “mass loaded vinyl” sheeting… It might be that I’ll have to apply it to the exterior for the best coverage. Does it appear to be that case that the only air inlet for the machine is via the “deflate” nozzle? I wonder how they deal with the machine over-heating as there does not appear to even be any ventilation holes.
I don’t feel like there is enough room inside the case to limit the noise. Most of it comes from the second stage piston pump (see video) and the noise also escapes through the air inlet which you can’t really block. In terms of heat, I believe these pumps don’t really have an issue with the additional heat but the case does get almost too hot to touch (especially closer to the air connectors).
A better approach might be to build a “dog-house” type of insulated box (one side open) that you place over the pump and direct that opening away from whatever is sensitive to the noise. Do share what you build!
Thanks so much. I did build a sound box for the pump. In tests inside, it lowered sound 30 db. When I used it outside at the lake, it lowered it quite a bit, but was still very loud for my tastes. I’m not sure how to post a picture of my box, but I have: an exterior of 5/8″ particle board, with caulked joints; then a layer of 1/2″ closed cell foam (like that which came in the Puffer Pro case; then a layer of self-stick, mass loaded vinyl (1/2lb? or 1lb?) with foil backing, and then a thin layer (1/16″) self stick foam. The lid is a removed wall, with foam gasketing. I need to study how sound must be leaking out of the instake/exhaust holes of the box first. I’m thinking, some insulated “sleeves” (like interior sound insulated air ducting) might be next step. Solving acoustic transmission problems is as difficult as trying to dam water, but it’s a fun problem. Now I’ve got “error 4” (EE4). I’ve written to manufacturer, but I’ll try draining the battery also.
Thanks for sharing the build and the findings! For sharing images you could upload it to any image sharing site and then add the URL here.
I wonder what the EE4 error stands for?
Hi. Automatic switch between simple fan and high pressure occurs at ~0.7-0.8 psi. Do you know is it possible to increase this value? The valve of my wing is quite tight and requires a little bit more pressure to open, so the pump switches to high pressure too yearly ( there is the pressure in hose but the air is not flowing though the valve ). The only workaround I found is forcefully switch to fan mode first and when it is done I’m switching back to auto.
I’m using the same trick. Not sure if there is a way to edit that setting.
A friend brought me one to look at as the case cooling fan would not stop running. Yours does not have this. For pics see: https://golbornevintageradio.co.uk/forum/showthread.php?tid=9434
This is what I did for him in a write up and giving it back.
The pump is two stages. Motor top right (your first pic) drives a simple fan that gives airflow to the piston pump left. This is driven by the motor, middle left, I didnt get this to run or draw current all out on the bench. Kasper’ blog indicates there is a low psi setting and it runs in the higher setting above 0.8 psi. Even back in the case and set above 0.8 psi I wasnt sure it was working. I didnt have the operating instructions.
The driver device for the cooling fan has gone short circuit so it was on all the time. Being surface mount this cant be repaired without specialist equipment and circuit and layout details. What I have done is wire this in shunt with the top right motor.. When this runs so does the fan which only takes 120 mA. Note it wouldnt run if the high pressure pump runs alone but I believe this doesnt happen. Also, it wont run during battery charging so take care. We have all seen these batteries catching fire on TV.
On the Blog he has the following:
“… but the case does get almost too hot to touch (especially closer to the air connectors).”
“… need to replace the circuit board which started to melt the USB terminals it totally overheated could’ve even caught fire.”
This is maybe the reason of fitting the case fan. It is very tiny and I could blow as hard … but not for so long.
Note: No case fan is shown in Kaspars version and the circuit board is different.
The currents involved are large and would not have been possible before modern Lithium batteries. I measured the top right motor drawing 7 A plus when it settled down. Kasper says the piston motor takes less at 4 A..
Somewhere I picked up that the unit should not be run for more than 30 mins. Its surprising with those current drains that it can manage this long.
Hello, My Airbank was not holding a charge for more than 2 days. I contacted the manufacturer and they said to leave it on the charger for 24 hours. I did a test run and pumped up 3 wings and a inflatable board. This brought the charge down to 2 bars. I connected it back to the charger and left it overnight. The next day I removed it from the charger and let it sit. I came back about 4 hours later and noticed a faint ticking sound similar to a clock. I opened the unit and noticed the small vent fan was constantly cycling on and off (76 times per minute). I believe this is what is draining the battery over the course of 3 to 4 days. Is there a way to stop this? Thank you.
New puffer Pro now has Quick Charge and the board has conformal coating
That’s great to hear! Do you have photos that you could share? Which version of QC does it support? Is it different from what I shared in the post?